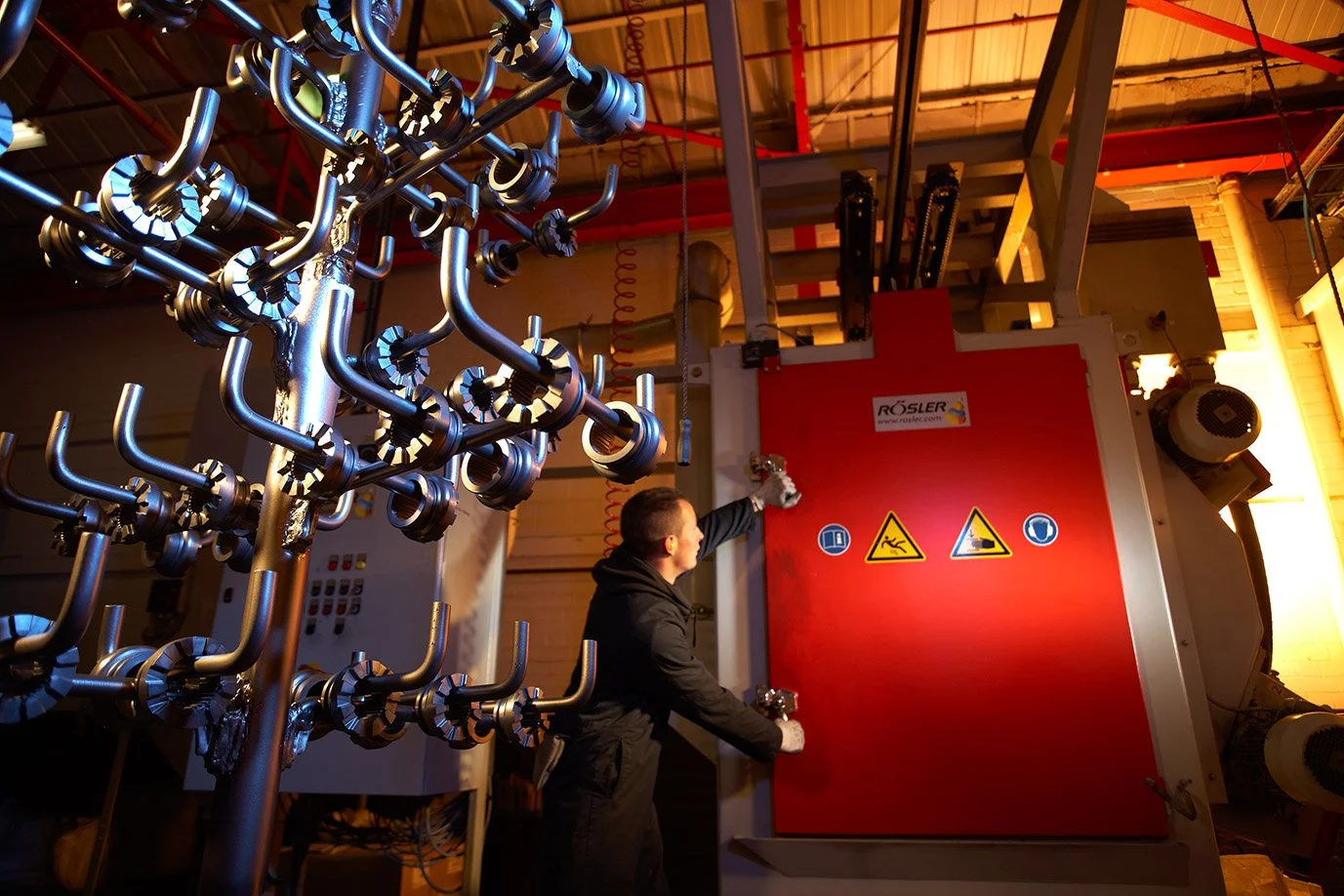
Surface Treatments
Welcome to the Metal Makeover Show, where metals get the star treatment to shine, toughen up, and be their best selves. Let's meet our contestants and see how they transform with a little TLC from surface treatments!
-
Shot peening is a cold working process used to improve the mechanical properties and extend the lifespan of metal components by introducing residual compressive stresses on their surfaces. This is achieved by bombarding the surface of the material with small spherical media called shots. The impact of the shots creates tiny indentations or dimples on the surface, causing the surface layer to plastically deform and compress.
Steps in the Shot Peening Process
Preparation: The part to be treated is cleaned to remove any dirt, oil, or other contaminants that might interfere with the shot peening process.
Shot Selection: The type, size, and hardness of the shots are chosen based on the material of the part and the desired results. Shots can be made from various materials, including steel, glass, or ceramic.
Peening Process: The shots are propelled onto the surface of the part at high velocity using a controlled air blast or centrifugal wheel. The coverage is usually uniform, ensuring that the entire surface receives the same treatment.
Impact and Deformation: As the shots strike the surface, they create numerous small indentations. The material below the indentations is compressed and plastically deformed, generating residual compressive stresses. These stresses are beneficial because they counteract tensile stresses that can lead to fatigue failure.
Inspection: After peening, the part is inspected to ensure that it meets the required specifications. This may include checking the surface coverage, intensity, and depth of the compressive layer.
Advantages of Shot Peening
Increased Fatigue Life: The residual compressive stresses introduced by shot peening significantly improve the fatigue strength of the component, delaying the initiation and growth of fatigue cracks.
Enhanced Wear Resistance: Shot peening can increase surface hardness, improving wear resistance and reducing the risk of surface damage.
Stress Corrosion Cracking Resistance: The compressive stresses help to prevent the initiation and propagation of stress corrosion cracks.
Improved Mechanical Properties: Shot peening can improve the overall mechanical properties of the component, making it more robust and durable.
Applications
Shot peening is used in a variety of industries to enhance the performance and lifespan of metal components, including:
Aerospace: Aircraft landing gear, turbine blades, and structural components.
Automotive: Springs, gears, connecting rods, and crankshafts.
Manufacturing: Tools, dies, and molds.
Energy: Components in wind turbines, oil rigs, and power plants.
Summary
Shot peening is a mechanical process that enhances the durability and performance of metal components by introducing beneficial residual compressive stresses. By bombarding the surface with small spherical shots, the process increases fatigue life, wear resistance, and resistance to stress corrosion cracking. It is widely used across various industries to extend the service life and reliability of critical parts.
-
Shot blasting is an abrasive surface treatment process used to clean, strengthen, or polish metal and other materials. It involves propelling abrasive particles (shots) at high velocity against a surface to remove contaminants, scale, rust, or old coatings. The process also improves the surface profile, making it suitable for subsequent treatments like painting or coating.
Steps in the Shot Blasting Process
Preparation: The part to be treated is cleaned to remove any loose dirt or oil that might interfere with the blasting process.
Shot Selection: The type, size, and hardness of the shots are chosen based on the material of the part and the desired results. Shots can be made from various materials, including steel, glass beads, aluminum oxide, or silicon carbide.
Blasting Process: The shots are propelled at the surface of the part using either:
Air Blasting: Where compressed air is used to propel the shots.
Wheel Blasting: Where a spinning wheel propels the shots at high velocity.
Impact and Cleaning: As the shots strike the surface, they remove surface contaminants such as rust, scale, old paint, or other coatings. The impact of the shots also helps to create a roughened surface profile, which improves the adhesion of subsequent coatings or treatments.
Recovery and Recycling: The spent shots and debris are collected, separated, and often recycled for reuse in the blasting process. Proper filtration and cleaning systems are used to maintain the effectiveness of the shots.
Inspection: After blasting, the part is inspected to ensure that it meets the required cleanliness and surface profile specifications.
Types of Shot Blasting
Sand Blasting: Uses sand particles as the abrasive media. It is less commonly used now due to health concerns related to silica dust.
Grit Blasting: Uses angular abrasive particles (grit) to create a rougher surface profile. Commonly used for heavy-duty cleaning and preparation.
Bead Blasting: Uses spherical beads, typically glass or ceramic, to clean surfaces and create a smooth finish.
Shot Peening: Similar to shot blasting but with the primary aim of inducing compressive stresses to improve fatigue strength.
Advantages of Shot Blasting
Effective Cleaning: Removes rust, scale, old paint, and other contaminants efficiently.
Surface Preparation: Creates a roughened surface profile that improves the adhesion of paints, coatings, and adhesives.
Surface Strengthening: Increases the surface hardness and wear resistance of the material.
Versatility: Suitable for a wide range of materials, including metals, glass, plastics, and composites.
Applications
Shot blasting is used in a variety of industries, including:
Automotive: Cleaning engine components, chassis parts, and restoring old car parts.
Construction: Preparing steel structures, bridges, and reinforcing bars for coating.
Manufacturing: Cleaning castings, forgings, and welded parts.
Aerospace: Cleaning turbine blades, landing gear, and structural components.
Shipbuilding: Cleaning and preparing ship hulls for painting and coating.
Summary
Shot blasting is an abrasive surface treatment process that cleans, strengthens, and prepares surfaces by propelling abrasive particles at high velocity. It effectively removes contaminants and creates a suitable surface profile for subsequent treatments. The process is versatile and widely used across various industries to enhance the performance and lifespan of metal and other materials.
-
Wet bead blasting is an advanced abrasive blasting process that uses a mixture of water and abrasive media (beads) to clean, polish, or finish surfaces. This method is particularly effective for delicate or precision parts, as it reduces dust and heat generation, leading to a finer finish and less damage to the substrate.
Steps in the Wet Bead Blasting Process
Preparation: The part to be treated is cleaned to remove any loose dirt, oil, or contaminants that might interfere with the blasting process.
Bead and Water Mixture: A slurry of water and abrasive beads, typically made of glass, ceramic, or other materials, is prepared. The water acts as a cushion, reducing the impact force of the beads and preventing surface damage.
Blasting Process: The slurry is propelled at the surface of the part using compressed air or a pump. The mixture is delivered through a nozzle at high velocity, impacting the surface to achieve the desired cleaning, polishing, or finishing effect.
Impact and Cleaning: As the beads strike the surface, they remove contaminants such as rust, scale, paint, or other coatings. The water helps to wash away debris and reduces dust, leading to a cleaner process and a smoother finish.
Recovery and Recycling: The spent slurry is collected, and the abrasive beads are separated, cleaned, and often recycled for reuse. Proper filtration systems are used to maintain the effectiveness of the slurry.
Inspection: After blasting, the part is inspected to ensure it meets the required cleanliness and surface finish specifications.
Advantages of Wet Bead Blasting
Fine Finish: Provides a smoother and more refined surface finish compared to dry blasting, making it ideal for precision parts.
Reduced Dust: The presence of water minimizes dust generation, creating a cleaner and safer working environment.
Lower Heat Generation: The water reduces friction and heat buildup, preventing warping or damage to delicate parts.
Versatility: Can be used on a wide range of materials, including metals, plastics, glass, and composites.
Environmentally Friendly: Uses water as a medium, reducing the need for chemical cleaning agents and minimizing environmental impact.
Applications
Wet bead blasting is widely used in industries where a fine finish and precision are essential, including:
Aerospace: Cleaning and finishing turbine blades, engine components, and structural parts.
Automotive: Restoring classic car parts, cleaning engine components, and preparing surfaces for painting.
Manufacturing: Polishing molds, dies, and precision machined parts.
Medical Devices: Cleaning and finishing surgical instruments, implants, and other medical components.
Electronics: Cleaning and preparing electronic components and housings.
Summary
Wet bead blasting is an effective and versatile surface treatment process that combines water and abrasive beads to clean, polish, or finish surfaces. It provides a fine finish with reduced dust and heat generation, making it ideal for precision and delicate parts. Widely used in various industries, wet bead blasting enhances the performance and appearance of components while maintaining a clean and environmentally friendly process.
-
Phosphating is a chemical process used to treat metal surfaces, providing corrosion resistance, improved adhesion for subsequent coatings, and reduced friction. It involves applying a phosphate coating to the surface of the metal through a chemical reaction between the metal, a phosphate solution, and an activator. Phosphating is widely used in the automotive, aerospace, and industrial sectors for surface preparation and protection.
Steps in the Phosphating Process
1. Cleaning: The metal surface is thoroughly cleaned to remove dirt, oil, grease, rust, or any other contaminants that could interfere with the phosphating process. This cleaning is often done using alkaline cleaners or degreasers, followed by rinsing with water.
2. Surface Preparation: The cleaned metal surface may undergo additional preparation steps, such as pickling with an acid solution to remove any remaining oxides or scale, followed by another rinse.
3. Phosphating: The prepared metal surface is immersed in or sprayed with a phosphating solution, which typically contains metal phosphate salts (such as zinc, manganese, or iron phosphates), phosphoric acid, and an activator. The solution reacts with the metal surface to form an insoluble phosphate layer.
4. Rinsing: After the phosphating treatment, the metal part is rinsed with water to remove any residual chemicals and ensure the uniformity of the phosphate coating.
5. Sealing (Optional): The phosphate-coated surface may be treated with a sealing solution to enhance corrosion resistance and improve adhesion for subsequent coatings or paints.
6. Drying: The treated part is dried to remove any remaining moisture, completing the phosphating process.
Types of Phosphate Coatings
1. Zinc Phosphate: Provides excellent corrosion resistance and is commonly used as a base for painting or powder coating.
2. Manganese Phosphate: Known for its wear resistance and is often used in applications involving friction, such as engine components and gears.
3. Iron Phosphate: Generally used for light corrosion protection and as a base for painting, suitable for less demanding applications.
Advantages of Phosphating
- Corrosion Resistance: The phosphate coating provides a barrier that protects the metal surface from oxidation and corrosion.
- Improved Adhesion: Enhances the adhesion of subsequent coatings, such as paint, powder coating, or lubricants.
- Wear Resistance: Reduces friction and wear on moving parts, extending the lifespan of components.
- Uniform Coating: Provides a consistent and uniform coating that covers the entire surface, including complex geometries.
Applications
Phosphating is used in various industries for a wide range of applications, including:
- Automotive: Treating body panels, engine components, and fasteners to improve corrosion resistance and paint adhesion.
- Aerospace: Preparing aircraft parts for painting and protecting against corrosion.
- Industrial: Coating machinery parts, tools, and equipment to enhance durability and performance.
- Consumer Goods: Treating metal furniture, appliances, and other products to improve appearance and longevity.
Summary
Phosphating is a chemical treatment process that enhances metal surfaces by providing corrosion resistance, improved adhesion for coatings, and reduced friction. It involves cleaning the metal, applying a phosphate solution to form a protective layer, and optionally sealing the surface. With various types of phosphate coatings available, such as zinc, manganese, and iron phosphates, phosphating is widely used in industries like automotive, aerospace, and manufacturing for its protective and preparatory benefits.
Capacities
Max Load | Max dimensions | |
---|---|---|
Air Nozzle Machines | ||
1 x 3 axis | 100kg | 1000mm x 500mm |
1 x 2 axis | 250kg | 900mm x 300mm |
1 x 1 axis | 100kg | 450mm x 50mm |
Shot Blasting | ||
2 x Hanging machines |