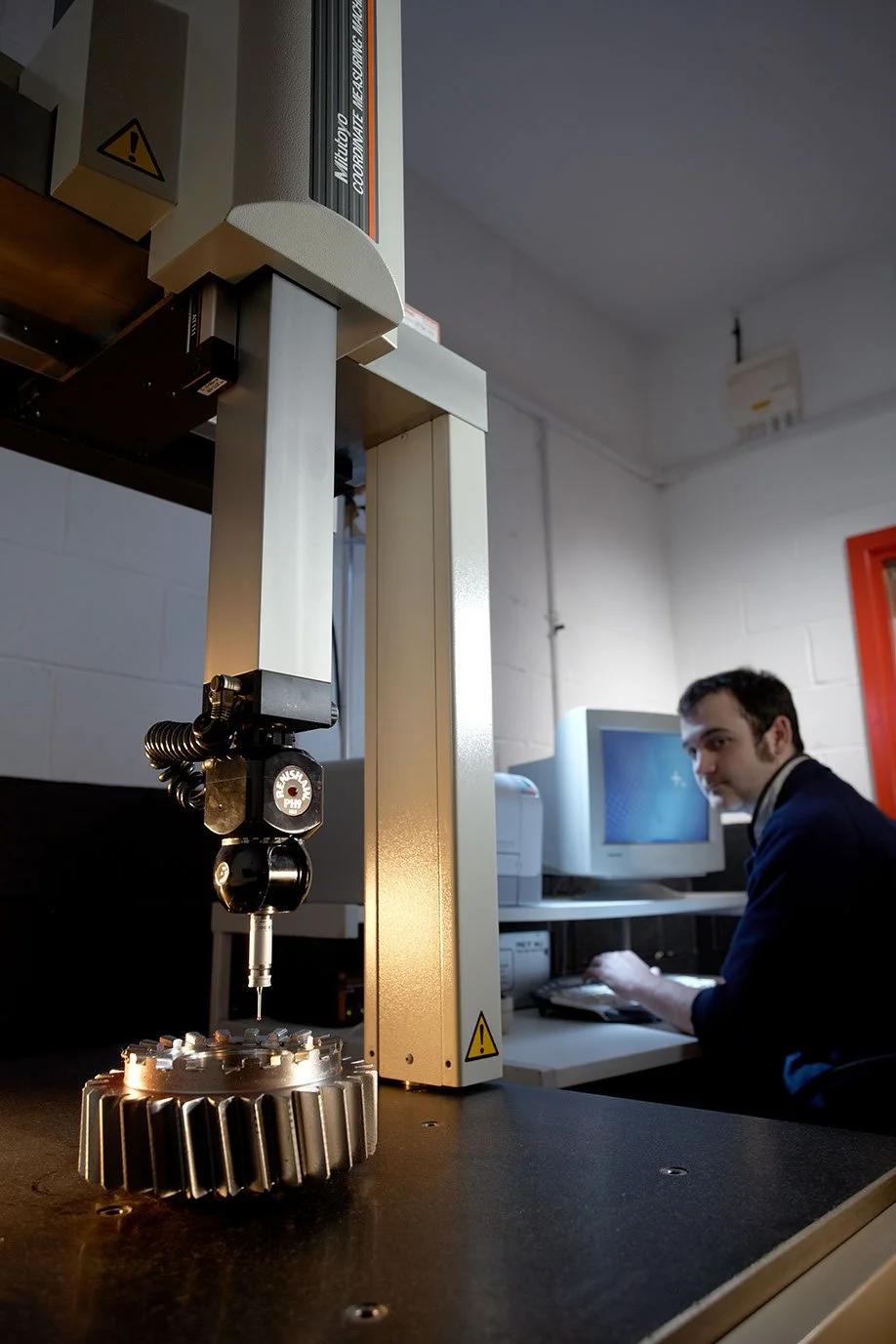
Laboratory
Our combination of metallurgical and metrological expertise in one lab creates a powerhouse of precision and material science. This dual approach ensures that not only are materials strong and reliable, but they are also manufactured and measured to exact specifications, crucial for the safety and performance of high-stakes industries.
Metallurgical
This section of the lab is dedicated to unlocking the mysteries of metals and alloys, ensuring they meet the rigorous demands of various industries.
Equipment and Setup:
Microscopes: High-powered instruments, including optical and electron microscopes, allow for detailed examination of metal microstructures.
Hardness Testers: Devices like Rockwell, Brinell, and Vickers testers that assess a metal’s resistance to indentation.
Sample Preparation Stations: Areas equipped for cutting, polishing, and etching metal samples to reveal their microstructure.
Key Activities:
Microstructure Analysis: Studying the grain structure and phases of metals to understand their properties and performance.
Mechanical Testing: Includes tensile, hardness, and impact testing to determine the strength, toughness, and ductility of metals.
Failure Analysis: Investigating the causes of metal failures to improve material selection and processing techniques.
Purpose and Impact:
Quality Assurance: Ensuring metals used in critical applications meet strict industry standards.
Metrological
This side of the lab is where measurement accuracy is king. Precision is everything, whether it’s ensuring components fit together perfectly or validating the dimensions of complex parts.
Equipment and Setup:
Coordinate Measuring Machines (CMMs): Advanced machines that use probes to measure the geometry of objects with extreme precision.
Optical Comparators: Devices that project the image of a part onto a screen, allowing for detailed comparison with design specifications.
Contour and Surface Stations: High-tech instruments that combine contour and roughness measurements in one system.
Calipers, Micrometers, and Gauges: Classic tools that provide precise measurements down to fractions of a millimeter.
Key Activities:
Dimensional Inspection: Verifying that parts conform to their specified dimensions and tolerances, ensuring perfect fit and function.
Calibration: Regularly checking and adjusting instruments to maintain their accuracy, a crucial part of quality control.
Surface Finish Analysis: Measuring the texture of surfaces to ensure they meet required specifications, affecting everything from friction to aesthetics.
Purpose and Impact:
Quality Control: Providing the precise measurements needed to manufacture parts that meet exacting standards, essential for everything from medical devices to automotive components.
Process Improvement: Data from metrology is used to refine manufacturing processes, reducing waste and increasing efficiency.
Certification and Compliance: Ensuring products meet regulatory standards and customer specifications, vital for industries like aerospace and defense.