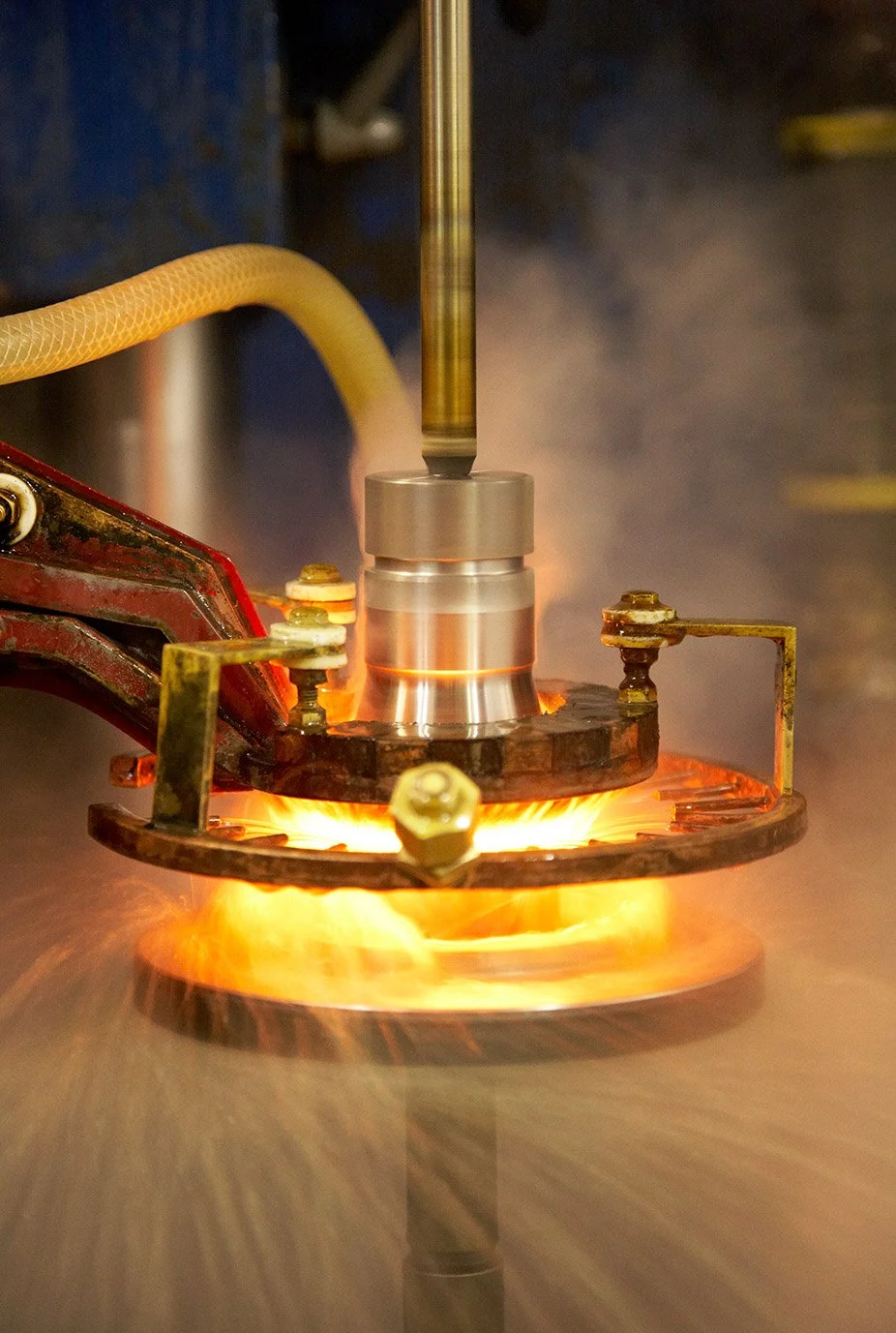
Induction Hardening
Picture this: your trusty piece of metal is gearing up for a superhero transformation, ready to become tougher, stronger, and more resilient. Welcome to the world of induction hardening – the ultimate metal power-up!
Induction hardening is a heat treatment process used to increase the hardness and wear resistance of a metal part, typically steel, by inducing a rapid surface heating followed by immediate quenching. This process selectively hardens only the surface layer of the part, leaving the core material unaffected and maintaining its ductility and toughness.
Steps in the Induction Hardening Process
Preparation: The part to be hardened is cleaned to remove any surface contaminants that could affect the heating process.
Induction Heating: The part is placed within a coil that generates an alternating magnetic field. The alternating current passing through the coil induces eddy currents within the surface layer of the part, causing it to heat rapidly. The depth of heating depends on the frequency of the alternating current; higher frequencies result in shallower heating depths.
Austenitizing: The surface layer is heated to its austenitizing temperature, typically between 800°C and 1000°C (1472°F to 1832°F) for steel. At this temperature, the steel's microstructure transforms into austenite, a phase capable of dissolving more carbon.
Quenching: Immediately after heating, the part is rapidly cooled by quenching, usually with water, oil, or a polymer-based quenching medium. This rapid cooling transforms the austenitic surface layer into martensite, a hard and brittle microstructure, while the core remains relatively unaffected.
Tempering (Optional): The hardened part may undergo tempering, a reheating process to a lower temperature, to reduce brittleness and relieve internal stresses without significantly reducing hardness.
Advantages of Induction Hardening
Selective Hardening: Only the surface layer is hardened, preserving the core's ductility and toughness.
Rapid Process: Induction heating is very fast, which increases production efficiency.
Precision: The process can be precisely controlled to harden specific areas or shapes.
Minimal Distortion: The rapid heating and cooling minimize distortion and reduce the need for subsequent machining.
Improved Wear Resistance: The hardened surface significantly increases wear resistance and fatigue strength.
Applications
Induction hardening is widely used for components that require a hard, wear-resistant surface and a tough core, including:
Automotive Parts: Gears, camshafts, crankshafts, and drive shafts.
Machine Tools: Cutting tools, dies, and punches.
Industrial Equipment: Rollers, shafts, and spindles.
Construction Machinery: Excavator teeth, track pins, and bushings.
Summary
Induction hardening is a targeted heat treatment process that uses electromagnetic induction to rapidly heat and harden the surface layer of a metal part. This process increases wear resistance and fatigue strength while maintaining the core's toughness. It is a precise and efficient method suitable for various industrial applications, especially where surface durability and core flexibility are essential.
Capacities
Machines | Power Supply | Frequency |
---|---|---|
1 | 10kW | 5kHz |
1 | 150kW | 10kHz |
1 | 450kW | 7-10kHz |
2 | 75kW | 7kHz |
A comprehensive range of fixtures is available to process gears and shafts
Max Heat Treated Length: 900mm
Max Diameter: 300mm